
How Is Stainless Steel Made?
Raw Materials
Stainless steel is an iron alloy with added elements such as chromium, nickel, silicon, manganese, nitrogen and carbon. The properties of the final alloy can be fine-tuned by altering the amounts of the various elements.
The Importance of Chromium in Making Stainless Steel
Chromium is essential for the production of stainless steel; in fact there’s no viable alternative. Chromium is a hard, corrosion-resistant transition element that gives stainless steel its corrosion resistance. In general, the higher the chromium content, the more corrosion-resistant the steel.
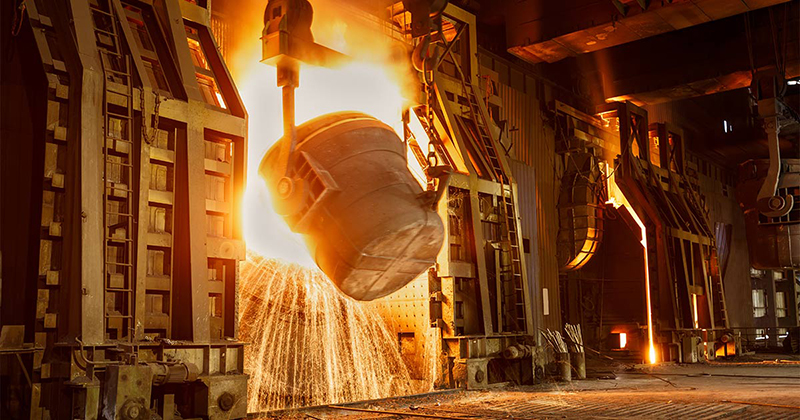
THE MANUFACTURING PROCESS
-
- 01
-
Melting
The raw materials are melted together in an electric arc furnace. It can take 8 to 12 hours of intense heat until the metal becomes molten.
-
- 02
-
Removal of Carbon Content
The next stage is to remove excess carbon. This is done by processing the molten metal in an AOD (Argon Oxygen Decarburization) converter. The converter reduces the carbon by injecting an oxygen-argon mixture. At this stage, further alloying elements like nickel and molybdenum can be added to the AOD converter.Alternatively a VOD (Vacuum Oxygen Decarburization) converter can be used to when a very low carbon content is required.
-
- 03
-
Tuning
Most stainless steels have exacting quality requirements. The tuning process allows fine adjustments to the chemical composition. Tuning is when the steel is slowly stirred to remove unwanted elements and improve consistency, while maintaining the required composition within the temperature limits.
-
- 04
-
Forming
Now the molten steel is cast into forms. These forms can be blooms (rectangular shapes), billets (round or square shapes), slabs, rods or tubes.
-
- 05
-
Hot Rolling
Hot rolling occurs at a temperature above the recrystallization temperature of the steel. The precise temperature depends on the desired stainless steel grade. The steel forms are heated and passed through high rolls. Blooms and billets are formed into bar and wire. Slabs are formed into plate, strip, and sheet.
-
- 06
-
Cold Rolling
Cold rolling is used where extremely precise dimensions or an attractive finish are required. The process occurs below the recrystallization temperature of the steel. Cold rolling is carried out using small-diameter rolls and a series of supporting rolls. This process allows the production of wide sheets with improved surface finishes.
-
- 07
-
Annealing
Annealing is the process used to soften stainless steel, improve ductility, and refine grain structure. It is also used to relieve internal stresses in the metal caused by previous processing. During the annealing process the steel is heated and cooled under controlled conditions.
-
- 08
-
Descaling
The annealing process causes scale to form on the steel. These scales are commonly removed using pickling, which involves bathing the steel in nitric-hydrofluoric acid. Electrocleaning is an alternative method which uses an electric current to remove the scale.
-
- 09
-
Cutting
The stainless steel can now be cut to the desired size. Mechanical cutting is the most common method. The stainless steel can be straight sheared with guillotine knives, circle sheared using circular knives, sawed using high-speed blades, or blanked with punches and dies. Other methods include flame cutting, which uses a flame-fired torch powered with oxygen, propane, and iron powder, or Plasma Jet cutting which uses an ionized gas column in conjunction with an electric arc to cut the metal.
-
- 10
-
Finishing
Surface finish is important for stainless steel products, especially in applications where appearances are important. While most people are familiar with the look of stainless steel used for consumer products, there are actually a number of finishing options.Grinding wheels or abrasive belts are commonly used to grind or polish the steel. Other methods include buffing with cloth wheels with abrasive particles, dry etching using sandblasting, and wet etching using acid solutions. The smooth surface provides better corrosion resistance.